New manufacturing techniques – 3D Printing for products and fixtures
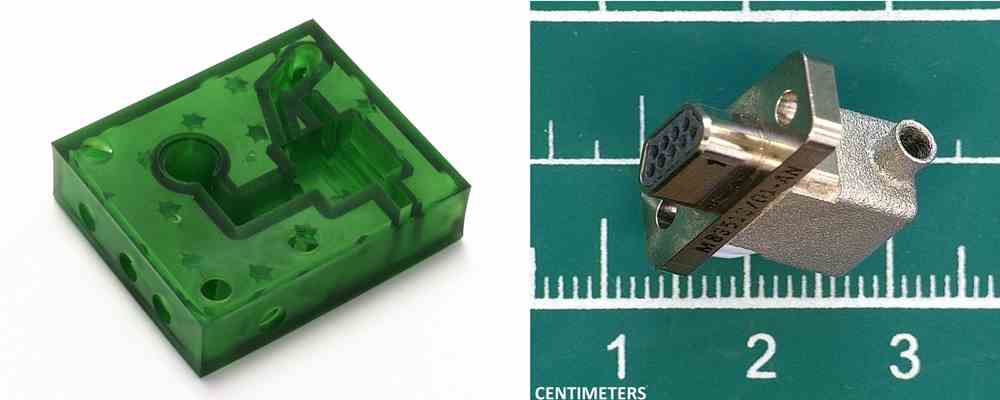
Pandect has increasingly been implementing 3D printing technologies to create jigs and fixtures for use in the manufacture and test of the products we design. 3D printing gives Pandect the flexibility to create and print parts quickly and in very cost-effective way. These fixtures greatly support our assembly workforce in many ways, from part holding to the verification of component orientation, improving both efficiency and repeatability.
One 3D printing method employed by Pandect uses Fusion Deposit Modelling (FDM) which can create components in several materials such as PLA, PETG & ABS. The printer can produce parts up to 270mm 200mm x 200mm and its purchase has greatly improved lead times compared with tools from our machine shop. An example of a fixture that we have made with FDM is shown in the first picture. This capability frees our machine shop to concentrate on specialisms, such as diamond turning. 3D Printing also allows us to make improvements to jigs and fixtures with ease, implementing changes suggested by shop floor technicians without the concern about high scrap and remanufacture costs.
The success of the FDM printing capability in Pandect prompted further research into 3D printing and more specifically Masked Stereolithography Apparatus (MSLA) 3D Stereo lithography. Where the FDM technology is good for creating non-complex shapes and relatively large fixture pieces, the MSLA technology offers the ability to make intricate and highly detailed parts on a smaller scale. We use this technology to support skilled areas of production such a brush setting, where precision is paramount. The MSLA print bed size is a fraction of the size of the FDM, but the accuracy is unmatched with an XY resolution of 35um and layer heights of 10um. The resin Pandect uses in our MSLA printer is also a good electrical insulator which opened the possibilities to utilize this printer even more widely, such as in electrical testing.
We have also successfully prototyped components using the MSLA technology that have gone on to be manufactured in production using the metallic 3D printing equivalent which is called direct metal laser sintering (DMLS). An example of this is shown in the second picture. Our customer had chosen a specific very small connector that had to be connected to braided wire. The surface metal finish of the connector was such that a very high temperature would be needed to solder the braided wire to this, and our soldering experiments showed that this could damage the connector. Pandect’s solution was to prototype with MSLA an intermediate “boot” to go between the braided wire and the connector. Having proved the concept in MSLA we then had metal versions of the “boot” made by a DMLS subcontractor. We proved that we could efficiently both solder the braided wire to the DMLS “boot” and connect the DMLS “boot” to the tiny connector with metal-loaded epoxy.
More news
Questions? We'll put you on the right path.
Contact Pandect
or call
Pandect Precision Components Ltd
+44(0)1494 526 303/4
Want to find out more about Pandect?